Now, mask factories in European and American countries are facing some pressure: on the one…
How to Produce Meltblown Fabric with High Filtration Efficiency and Low Breathing Resistance?
How do you value a good antiviral mask? From the long-time wearing experience, you can easily tell: those masks with high filtration efficiencies like N95 mask and at the same time make it very easy to breathe, exactly! And the key to achieve this goal is the melt-blown fabric. In this article, we will share some tips from the meltblown production line technicians who have been in the industry for decades.
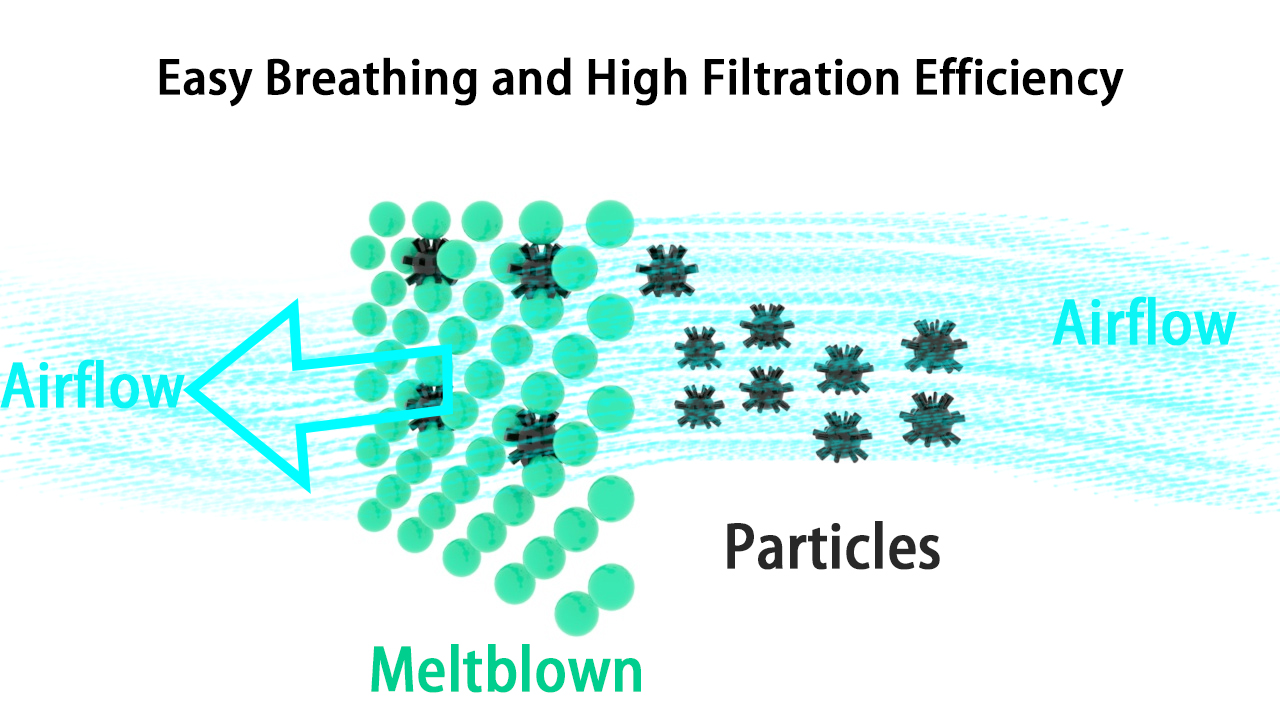
The manufacture of meltblown cloth production equipment is not complicated, the main thing to be overcome is the manufacturing process. Since there is a need to match parameters such as temperature, air pressure, mold, speed, etc., it is necessary to constantly grind and adjust the product to achieve the best results (according to the meltblown cloth core index test, with high filtration efficiency and low breathing resistance).
1. Methods to improve filtration efficiency
- Increased hot air flow or temperature (increased fibre fineness, reduced porosity, improved catching capacity but increased resistance).
- Increasing the electrostatic voltage (current) (polarizing the fibres, increasing the electrostatic field energy of the fibres and improving their adsorption capacity).
- Adding powder or other electrons to the raw material (to increase the chargeability and storage time of the fibres, allowing them to carry more charge and charge time).
- Increase the under-net suction (increase the density of the fibers and improve the ability of the fibers to catch. (Significantly larger grams, not commonly used).
- Appropriate reduction of production (with the same process, the amount of extrusion becomes smaller, the fibre becomes thinner and the resistance increases).
- Increase the working temperature of the die head (tip), etc. (better melt flow, thinner fibres).
- Increasing the ambient temperature of the spinning (fibre thinning, generally at higher room temperature, with a more pronounced increase in resistance and a decrease in other physical indicators).
- Increase the amount of powder to be added as appropriate.
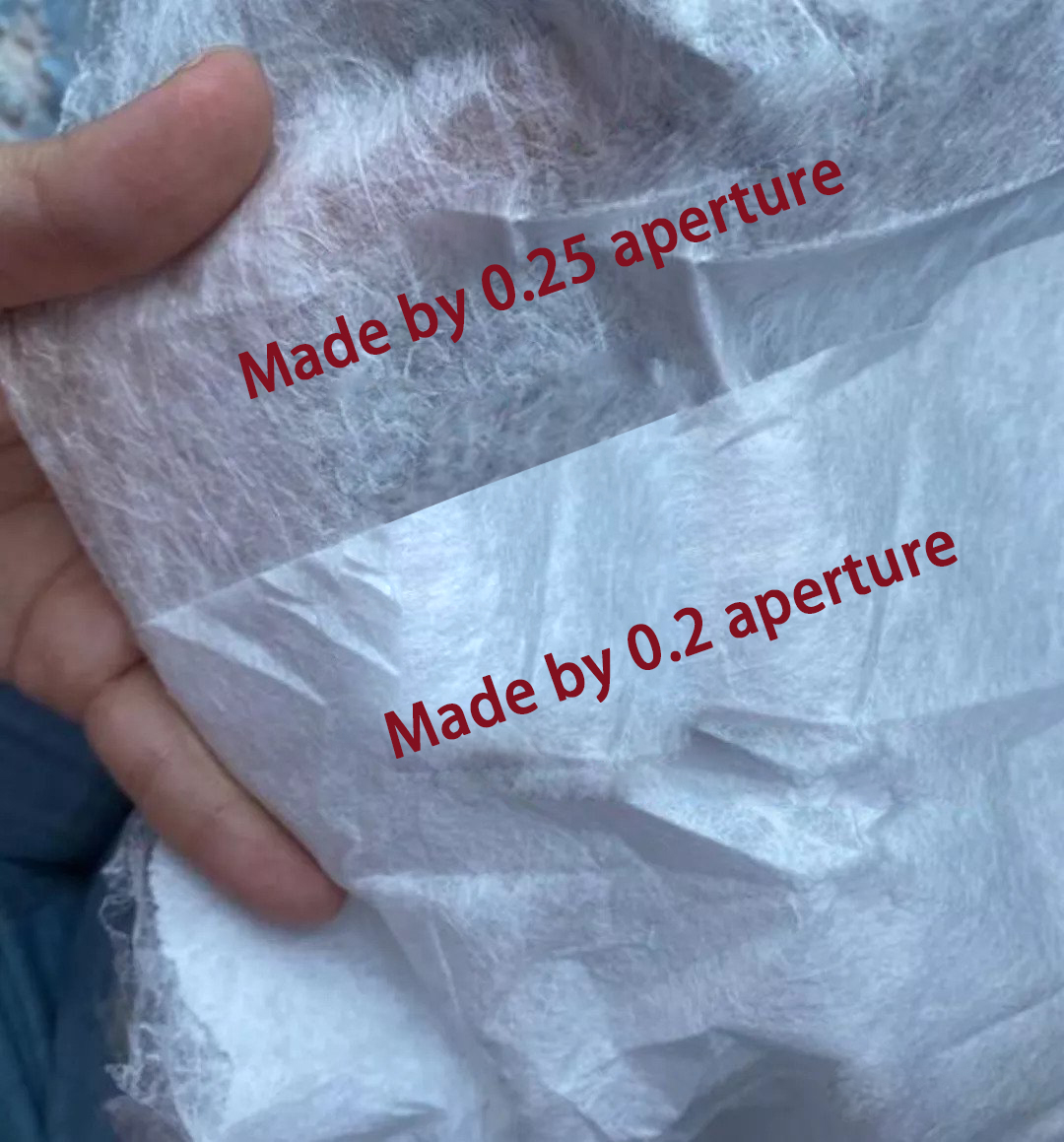
2. Methods of reducing resistance
- Reduction in hot air flow or temperature (coarsening of fibres, high porosity, low resistance and reduced efficiency).
- Increasing DCD (increased fluffiness of fibres, high porosity and reduced efficiency).
- Reducing the ambient temperature of spinning (adequate cooling of fibres, fluffy structure, increased porosity, with hot air to reduce resistance and improve efficiency).
- Reducing under-wire suction (dense to fluffy fibres, greater porosity, more pronounced large weight).
- Reducing the working temperature of the heating zone such as the die head (tip) (thickening of the fibres and increasing porosity).
- Increase in metering pumps (coarsening of the extruded fibre and increase in porosity, generally used in fast-turning orders).
- Appropriate reduction in grams (within the scope of internal control).
3. Methods that can reduce resistance and improve efficiency at the same time
- Increase the DCD and at the same time, increase the hot air flow or temperature, as appropriate, to reduce the air absorption at the bottom of the net (increase the fineness and fluffiness of the fibres).
- Improving fibre fineness while reducing the ambient temperature of the spinning (e.g. by adding cold air units).
- Improve the fluffiness of the fibres and at the same time, increase the electrostatic voltage (current) and increase the amount of powder added as appropriate.
- Increase the fineness of the fibre and reduce the gram weight appropriately (not commonly used).
Wish you find this information useful, If you want to purchase rather than produce this kind of meltblown fabric with high filtration efficiency and low breathing resistance to produce antiviral masks, please check this page. We supply high-quality mask raw materials tested with our mask testing instruments.
This Post Has 0 Comments